URL: https://www.desy.de/news/news_search/index_eng.html
Breadcrumb Navigation
DESY News: First live images of stress in materials using synchrotron radiation
News
News from the DESY research centre
First live images of stress in materials using synchrotron radiation
Researchers at DESY's synchrotron radiation source PETRA III have for the first time succeeded in visualizing stress fields within microscopically thin layers of metal based ceramics in situ. A new technique permits this unprecedented live view of the effects of a force being applied on an atomic scale. The necessary set-up at the nanofocus measuring station on the PETRA III beamline P03 was designed and installed by Christina Krywka of the Helmholtz Centre Geesthacht, in collaboration with her colleagues from the University of Leoben in Austria, specifically for measurements of this kind. The new technique could help to improve wear-resistant coatings for tools, for example.
The nanoindenter at PETRA beamline P03 allows live measurements of stress in thin layers.
For these high-precision experiments a so-called nano-indenter was used. For the in-situ experiment, not only the sample must be positioned precisely underneath the tip, while the latter accurately maintains the right amount of pressure; the entire tip and sample must, at the same time, be moved with microscopic precision relative to the X-ray beam. On top of this, no vibrations must be allowed to occur during these movements so as to maintain the high precision of the measurements.
Materials that exhibit extremely high resilience and strength are needed and used more and more often in our daily lives. The metal based ceramic material investigated here, titanium nitride, can be used as a thin protective coating of just a few microns, for example to harden tools. The service lifetime of a metal drill bit can be extended, so the drilling head can be exchanged less frequently. “The titanium nitride layer can be pre-stressed,” Krywka explains. “This means, the atomic structure of the crystal lattice is stressed so that it counteracts external pressure or slows the propagation of cracks.” It is rather like when you tense your muscles. If you press your finger into the relaxed muscle, it gives way; but if you flex the muscle briefly, you can clearly feel a resistance. The protective coating is thought to work along the same lines, making it harder to damage the drill bit while it is cutting holes in hard metals.
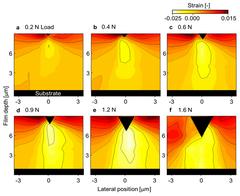
A set of measurements for such a live observation of the stress distribution in a material begins by measuring the unstressed sample. The sample is scanned in a 2D fashion by a tiny X-ray beam and diffraction patterns for each point are recorded. The beam then returns to its initial position, the diamond tip of the indenter is placed on the sample and a small force is applied, whereupon the sample underneath the tip is once again scanned. This procedure is repeated for different amounts of pressure, until data has been recorded for each position on the sample and for all the applied forces that are desired. It can take four to six hours before all the required points on the sample have been scanned and the data has been recorded.
The data now collected was analysed by the scientists at Leoben to make the actual stress fields visible. The data consists of so-called Debye-Scherrer rings. “If the sample were a single perfect crystal, in which all the atoms are aligned within the crystal lattice, you would only see individual Bragg reflections and no rings in the detector,” says Krywka. “But the sample actually consists of many tiny crystals, which have no preferential alignment.” Like grains of rice in a jar, the tiny crystals can be pointing in any direction. This so-called polycrystalline structure means that the countless reflections overlap in the detector to produce Debye-Scherrer rings.
When there are no stresses in the material, the detector displays perfect circles. However, if the crystal is subject to stress, the distances between the atoms will be larger or smaller than usual in certain directions, so that the circles are deformed into ellipses. And it is these distortions of the Debye-Scherrer rings that the researchers examine. The analysis of the distortions can be displayed in the form of contour lines, like on a topographical map. This map then reveals areas that are subject to compressive stresses and regions subject to tensile stresses, which are therefore susceptible to crack formation.
These stress maps – or stress fields – were then compared with numerical models. “So far, we have lacked the experimental data in order to verify numerical simulations of such thin layers,” Krywka explains. “These data will help us to improve the models and our understanding of this type of material, so as to develop even more hard-wearing coatings in the future.” A direct comparison between the model and the experiment shows that large-scale effects, such as cracks and other flaws, are correctly predicted by the model, however this was not true of the finer details. “This shows how valuable real-life measurements are,” says Christina Krywka. “What distinguishes our new method is that we are able to observe stresses that arise long before permanent damage occurs to the crystal lattice, such as a fracture. This will allow us to improve the existing models, which have only been able to take into account permanent damage.”